100 Years
100 Stories
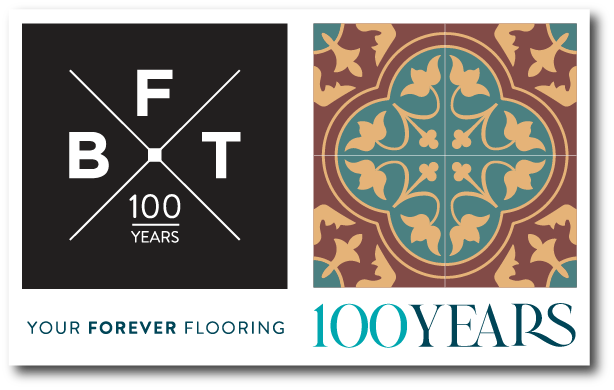
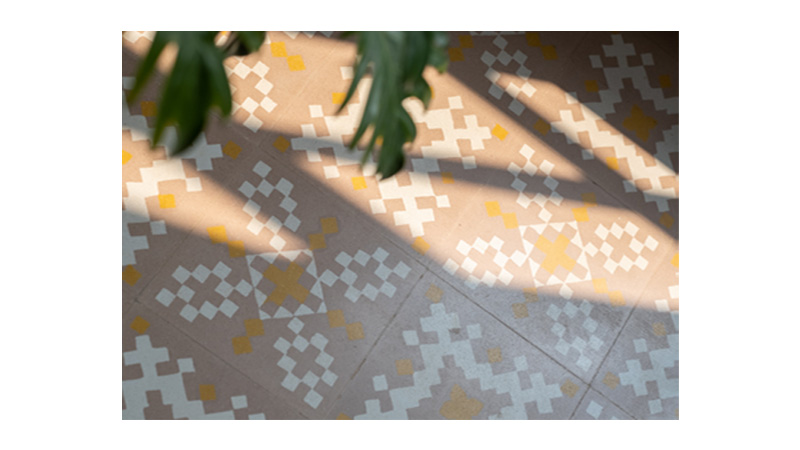
The Patola Pattern customised for Mody Design Studio.
Tracing the birth of a customised tile is an intriguing experience. Originating deep in the recesses of a client’s mind, it could be rooted in a stray train of thought, an impressionable pattern or a memory. From its origins in grey matter, to a computer screen in an office room where it is first designed, and eventually to the factory where it finally materialises, every step of the tile production is peppered with stories. For Bhakti Varekar, the in-house designer at BFT, transforming an emotion into a viable product is routine.
A qualified interior designer with a specialisation in flooring, Bhakti started working for BFT when it struck her that she was drawn to designing products rather than entire spaces. Bhakti’s first project was customising flooring for classrooms and corridors in a school set in a heritage structure in Bombay. And from there, she started working on a number of heritage projects, customising floors to match the original flooring and also creating unique tiles in a variety of shapes and colours to match the homeowner’s preference.
Although the creation of custom tiles is a closely guarded secret developed over time, luckily for us she is willing to share her secret and gives us a step-by-step guide through the work that goes into crafting Bharat's customised tiles.
One of BFT’s strengths has been the ability to create new designs as per the user’s wish. Why do you think this has been possible?
BFT has been making cement tiles for 100 years now. Our ability to understand the behaviour of the material i.e. cement, stretch its limits and produce a quality product are very high. For a hundred years we have both inspired and adapted to evolving trends in design and colour and so experimentation is part of our DNA. BFT works with specific designers for designing new ranges of tiles. But we also have a team of internal designers such as me who produce new designs and help homeowners in selecting and visualising their selected tiles in a given space. We also convert a vague concept or an idea of a client into a tactile everlasting visual.
At a surface level, it might appear that a tile can be made out of any design or motif. What determines the feasibility of a design?
The tile making process involves seven steps which combine art and science. These include making the moulds, colour mixing, colour-filling by hand, backing layer filling, right degree of pressing, wet curing and air curing. And then the laying and polishing is also an art and a science. Clients are usually unaware of our specifics which are unique because of the handmade process. The designs that you see are not printed or painted on the surface, they run deep and therefore the width of spaces to be filled with colour is a challenge. Fine lines for instance are a nightmare. One of my first jobs is to see if the preferred design is even possible in cement.
So, how do you meet the customer’s vision while working with the limitations of the product?
Let me explain this with an example. A client once reached out to us with a reference photograph of the floor he wanted. The design was inspired by delicate Spanish and Moroccan tiles and so there were many fine curved lines and arcs set close to each other. The design as is, would have been impossible to develop and with a high probability of wastage arising. We had to thus create a less complicated version of the design while ensuring that the basic aesthetic of the Spanish and Moroccan tiles was not compromised.
What about working with colours, which play a huge part in the overall appeal of the floor? The richness of these colours, as seen in some of the oldest floors, is everlasting.
We have over 30 colours – the original standard colours such as reds and yellows, white, black and grey; special shades of colours like the blues and greens and peach, as well as a new range of pastel shades for a modern palette. Since colour mixing is done in our own factory we can even play around with shades for large orders . Getting the right shade and having it approved by the client is an integral part of our process, but because of the variations in the shade of cement and of colours it is not a purely mechanical process and some final variation must be expected. While it is easy to visualise a tile in any colour, when it comes to actually executing the design, one has to keep in mind the bleeding of colours. For example, black and white combination is a common request among clients, however, in reality, it is difficult to execute a pattern in this combination since both colours tend to bleed into each other during the polishing process. The white does not come out milky white and so we recommended the use of off-whites, silver grey and creams.
Could you tell us about some of your favourite customised tiles that you've developed?
I’ve lost count of the new designs I've developed for BFT, but I can recall some of the more recent ones. We work closely with interior designers to make their vision a reality . The Topography tile for Satyajit Patwardhan, for instance, stands out in my memory. It was not a particularly challenging task since the designer’s artwork was simplistic, even though it was incredibly reflective of the home owner’s personal history. Patwardhan had taken inspiration from the client’s graphic designing background and created a flowing pattern with what looked like rough pencil sketches. Even though it was simplistic, the design in a two-colour scheme got rave reviews.
Another project we worked on was for Rishabh Modi, an architect and designer, who wanted the patola fabric from Gujarat to be recreated for his floor. Now, patola itself is intricate and impactful, resulting from a dizzyingly mathematical process. Modi picked the navratna bhat pattern, one of the most sought-after designs comprising a combination of tiny squares that form two sets of motifs on a fabric. There was no way we could achieve the scale of the design as seen in an actual patola fabric and so my job was to magnify the basic pattern in such a way that when spread across the floor, it reminds the viewer of the patola saree.
How long does it take to create a custom-designed tile?
The basic manufacturing time remains the same - 20-25 days. However, finalising the design and the colours can sometimes take upto one and half months as it sometimes involves creating samples as well. It took us nearly two months to design the tiles for the Shakti Mills showroom of Kohler sanitaryware in Bombay. Designed by ZZ architects, the flooring came together through a combination of thirty designs of different colours. We had to create ten stencils based on their artwork. It was quite difficult. We took one figure and assembled it into thirty blocks to create ten stencils. Each of these stencils was turned into a different tile. After all these efforts, a unique work of floor art emerges. And when the client is delighted, we are delighted !
You may also like
-
52Witness to Eminence: Darbhanga House, Mumbai My Home SeriesOnce home to the father of the Aarey Dairy farm, this lavish apartment has seen many an eminent personality grace its floors.Read More
-
53The Terrazzo RenaissanceHistory repeats itself as terrazzo makes a triumphant comeback in the world of interior decor, adding a burst of timeless elegance to modern spaces!Read More
-
54Unitinta: Plain but VersatileThe Plain Jane's got something to say ! See what the Unitinta or single coloured Bharat tile can do!Read More